The Secret to Precision: Sheet Metal Bending Accuracy Explained
- Laser Center
- Apr 18
- 1 min read
Hello from Laser Center!
This article explores the concept of bending deduction, a critical factor in achieving precision in sheet metal bending.
Bending deduction refers to the difference between the total length of the flat pattern and the combined length of the two flanges in a bent part. Simply put, it’s how much material is “lost” in the bend and must be accounted for during flat pattern development. Getting this value right is key to producing accurate parts that meet design specifications.
The bending deduction value changes depending on the material type, thickness, and the tooling used. If the deduction is off, even by a little, the final dimensions of your part can be wrong, leading to functional issues or wasted material.
To ensure consistent accuracy, we regularly perform test bends and record precise bending deduction values for different material grades and thicknesses. This data is then applied to every production run to maintain tight tolerances and reliable results.

Another important factor is material quality. Using inconsistent or low-grade sheet metal can lead to variations in how the metal reacts during bending. This can cause larger tolerances or angle deviations, potentially making parts unusable.
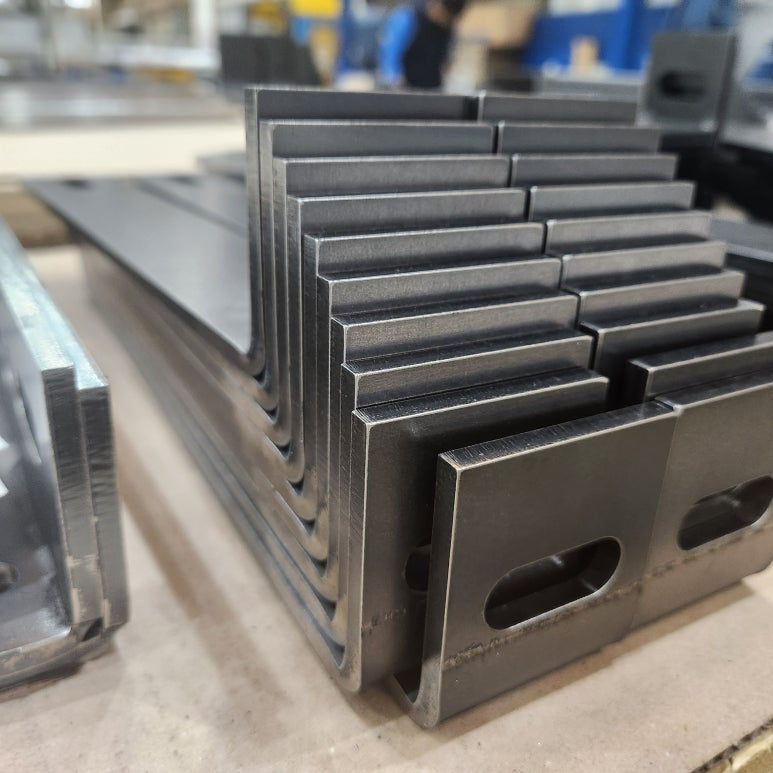
At Laser Center, we maintain a large inventory of certified, high-quality materials and apply accurate bending deductions to every job. Our attention to detail helps us deliver consistent, high-precision results, whether it’s a single prototype or a high-volume production order.
If you’re looking for a dependable partner for precision metal bending, Laser Center is here to help. Contact us today to learn more!
Comments